数字真皮“绿色”裁剪,用尽每一寸可用的皮料
2022年8月,某报告显示,从2020-2021年皮鞋行业运营情况来看,2021年中国皮面皮鞋制造企业数量为2122家。
可以说,在过去的30年里,随着全球化进程不断深入,我国已成为世界上名副其实的皮革生产大国。同时,运动休闲鞋中融合皮革材料是一大流行趋势,相关政策文件出台也引领了鞋类企业走上技术发展之路。
但在产业快速发展进程中,在这由消费者为导向的阶段下,各大皮鞋制造商面临的越来越多竞争压力与多方面的严苛要求。
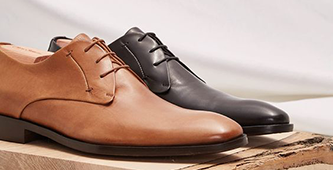
01
站在生产制造的角度
站在生产制造的角度,制造业亟需解决频现的“用工荒”问题、并应对持续高涨的原材料成本、充分考虑如何提升材料利用率,实现降本增效。
站在品牌方的角度
站在品牌方的角度,在各品牌方坚持创新,坚持以多样化、个性化产品迎合消费者的大趋势下,制造商不仅要积极调整思路适应品类繁多、订单大小不均衡的小批量订单,还要利用创新科技释放产能,应对短交货期的大批量订单,并具备创新能力。
站在企业管理的角度
站在企业管理的角度,如何建设数字化车间,引入精益管理,做到车间层面精准化计划、精益化生产、可视化展现、精细化管理,等等诸如此类的问题,都是制造商有效提升竞争力所需正视的挑战。
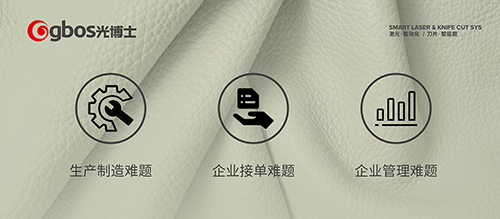
02
数字化转型迫在眉睫
以上种种对制造商的挑战与要求,无一不在阐明皮鞋业实施打造数字化生产车间,以提升企业核心竞争力的急迫性与必要性。而为什么越来越多的鞋业选择光博士一站式智能排版+裁剪解决方案,我们来一探究竟。
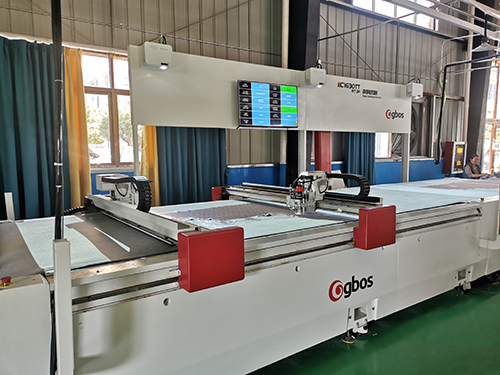
03
用尽每一寸可用的皮料
光博士数字化真皮排版+裁剪解决方案在鞋业市场得到了充分的验证,其在改变传统制造模式时,做到智能化生产与数字化管理深度融合,助力打造免模、省人工、省时省力的皮料生产模式。
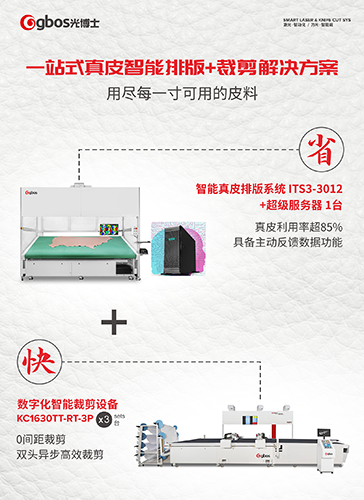
具体表现如下:
- 用尽每一寸可用的皮料:使用ITS3智能排版设备后,真皮排版时间约减少至3分钟左右/张,真皮排版利用率高达约85%及以上;真皮裁剪在实现0间距裁剪的同时,裁剪效率约8张皮革/小时;(数据仅供参考,实际数据根据裁片复杂程度而定)
- 极具灵活性的裁剪方案:在投影预览定位系统、真空吸附系统、多层送料系统及其它功能的助力下,不仅能完成真皮高效精准裁剪,还能完成PU, TPU等合成革的多层高效生产;
- 数据可视化管理,让你的智造车间脱颖而出:生产效率提升很大程度上需要实时、准确的数据支撑。光博士IoT Bridge以及OEE看板不仅可助力减少纸质化生产,在辅助管理决策上也有极大帮助。
若您的企业正探索皮革业如何打造数字化生产车间,光博士一站式智能排版+裁剪解决方案,正是助力您企业提升竞争力的不二之选。
未来,光博士将持续以“数字化”为导向,以助力企业“用尽每一寸可用的皮料”为内在驱动力,继续深耕皮革业技术创新、产业转型与产品持续升级的融合发展,全力推进智能化生产线、数字化管理车间等变革。