Driving Sustainability Green Auto Interiors
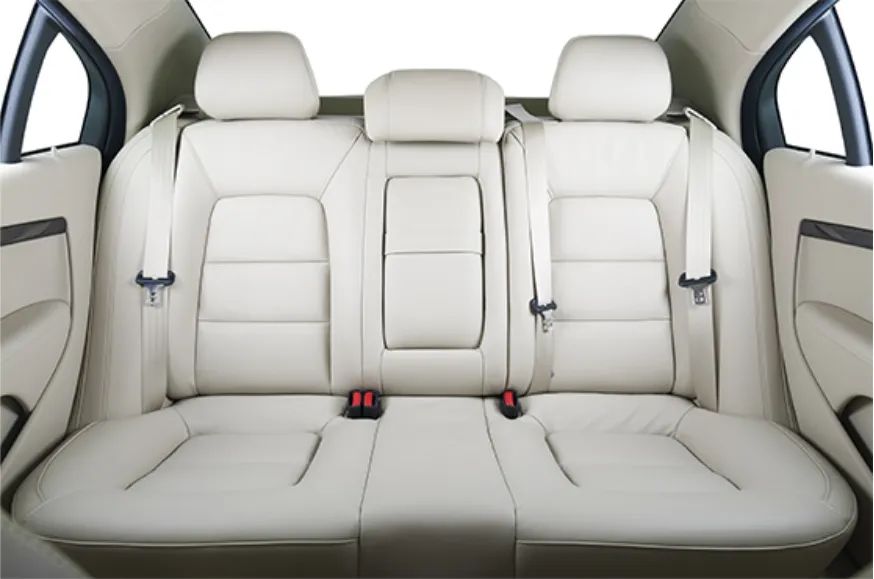
In this fast-moving era, automotive interior manufacturers bear a dual responsibility: to pursue the uniqueness and beauty of automotive interior design, while at the same time being responsible for our planet by reducing the environmental burden of the production process.
At this critical crossroads, GBOS has found a new path that combines environmental protection and efficiency, which will lead us to a more sustainable future. Now, let's take a deeper look at this change and see how it matters in terms of 0 waste and environmental innovation.
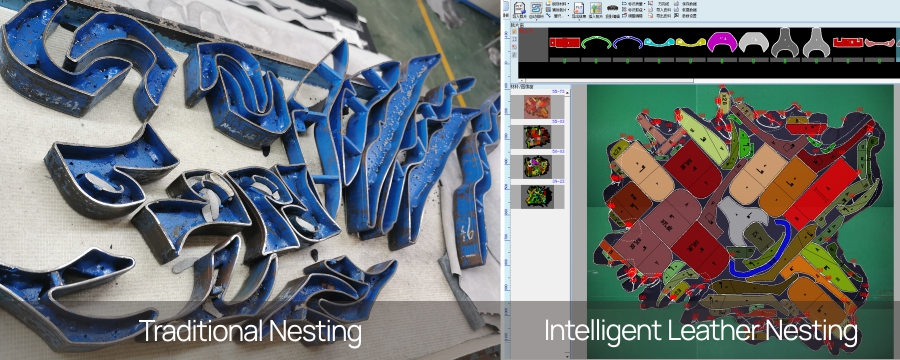
01 The Challenges of Traditional Leather Nesting
Traditional leather nesting methods suffer from a number of waste issues, mainly due to irregular cuts, variability in different parts and the limitations of manual nesting.
Due to the diversity of automotive interior design, traditional nesting often requires cutting irregular shapes, leading to greater material waste; fixed sizes and differences in leather characteristics of different parts also make it difficult to maximize the full use of materials during nesting; at the same time, the time pressure and complexity of manual nesting also increase the possibility of waste.
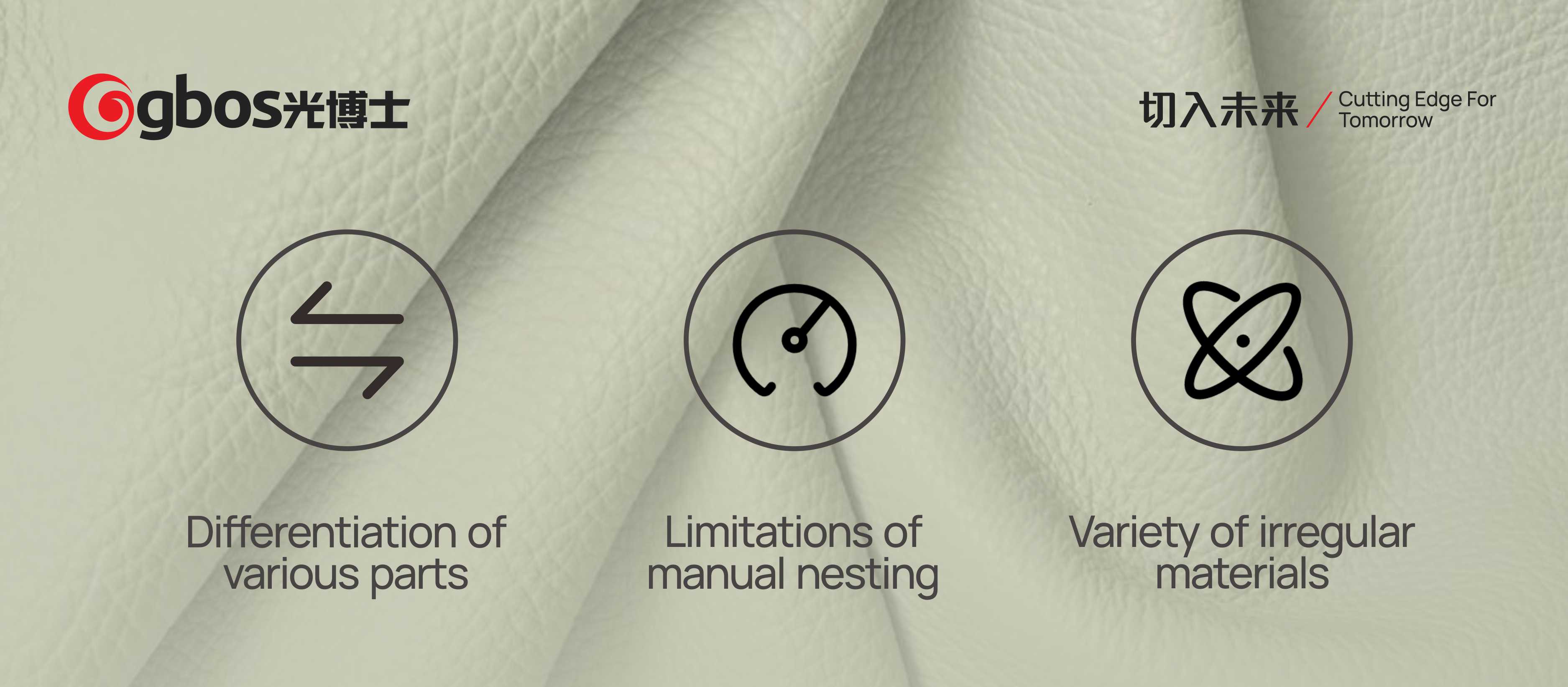
02 The Green Change of Intelligent Nesting
GBOS's intelligent leather nesting technology provides us with a more efficient and environmentally friendly solution. According to feedback, this technology can increase material utilization to 85% or higher, while also more accurately taking into account leather characteristics and part differences, thus further reducing waste and excessive pressure on natural resources, and injecting green innovation into leather nesting.
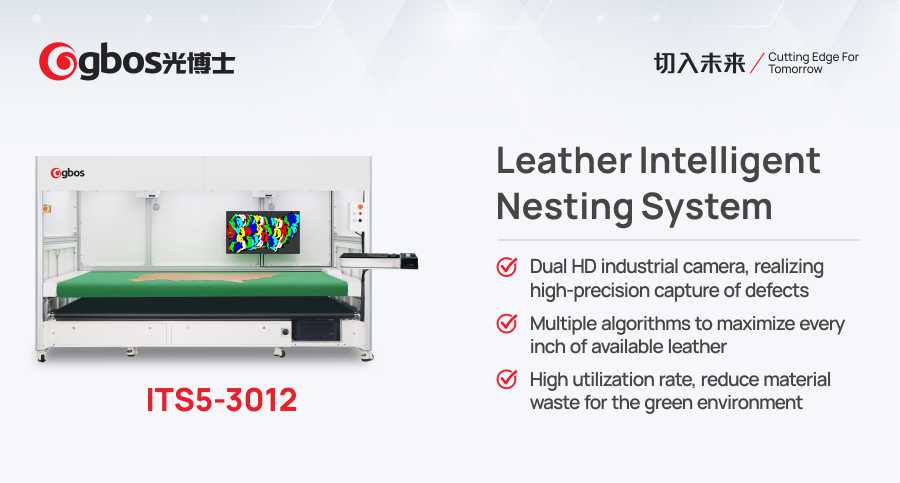
03 Environmental Contribution of Intelligent Cutting Technology
The traditional automotive interior cutting process requires a lot of manual operations, which not only increases costs, but also may lead to more material waste. The new intelligent leather cutting technology, on the other hand, offers a more efficient and environmentally friendly alternative. Using GBOS digital cutting technology can significantly reduce energy consumption and harmful emissions, pushing interior manufacturers towards a more sustainable development.
Expanding on this, the oscillating knife cutting technology, for every 10,000 knives, is able to reduce 120KWh of electricity, 119.64KG of CO2 emissions, 3.6KG of SO2 emissions, 62.64KG of carbon dust, and 1.8KG of NOX emissions. (Note: Reference data only, the actual data is subject to the cutting board size)
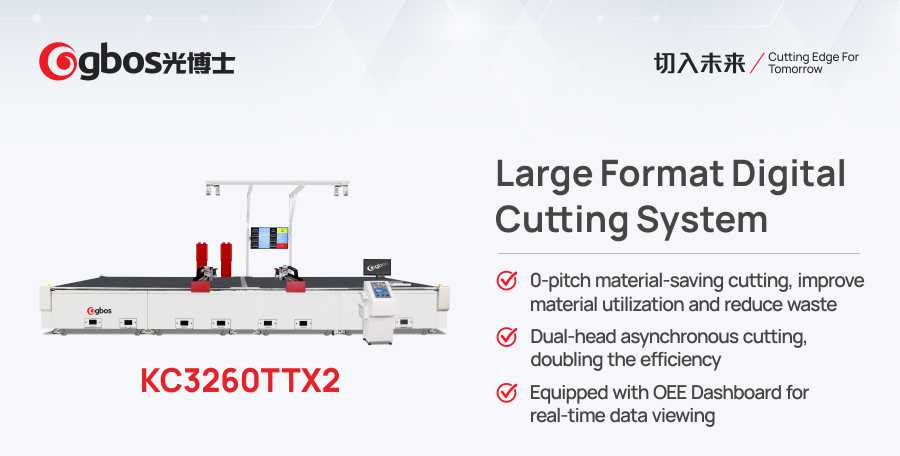
Overall, for automotive interior manufacturers, this is not just a technological update, but represents our strong commitment to green manufacturing and our fervent pursuit of a greener future for manufacturing.
Let's work together to create a greener and more sustainable future for the automotive interior manufacturing industry!
Professional Digital Cutting Solutions
Smart Layout Planning | Sample Testing | ROI Analysis | Technical Support | Training | Custom Solutions | Parts