Energy Savings = Profits: Reflections on the "High Energy Cost Pressure in Pakistani Textile Industry" Incident
Recently, the "High Energy Cost Pressure Facing the Pakistani Textile Industry" incident has sparked significant debate. According to analysts, the increase in natural gas rates has pushed the cost of electricity generation in backup power plants to over 45 Pakistani Rupees per unit, exceeding the current utility electricity rates for industries. This situation has exacerbated the energy crisis.
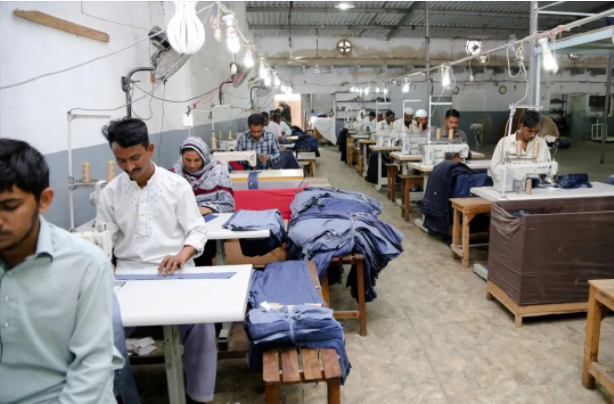
The high energy costs have made it challenging for some textile businesses to afford natural gas expenses, posing a threat to the survival of the garment manufacturing industry. By the end of 2023, according to APTMA reports, over 1,500 textile units were forced to shut down due to rising electricity and natural gas prices, resulting in decreased production efficiency becoming a reality.
In light of this incident, GBOS has several key reflections:
- Firstly, the textile industry should actively embrace lean management to reduce costs by improving electricity utilization efficiency, thereby enhancing competitiveness.
- Secondly, the broader energy challenges in Pakistan require deeper thinking and action. There is a need for more efforts to diversify energy sources, improve energy infrastructure, and reduce excessive reliance on limited resources.
- Lastly, for the textile industry, adopting more energy-efficient processes and equipment is an effective way to address the challenges of high energy costs. By introducing advanced production technologies and equipment, the textile industry can increase efficiency while reducing energy consumption, achieving sustainable development. This not only helps companies stay competitive but also alleviates the overall national energy burden.
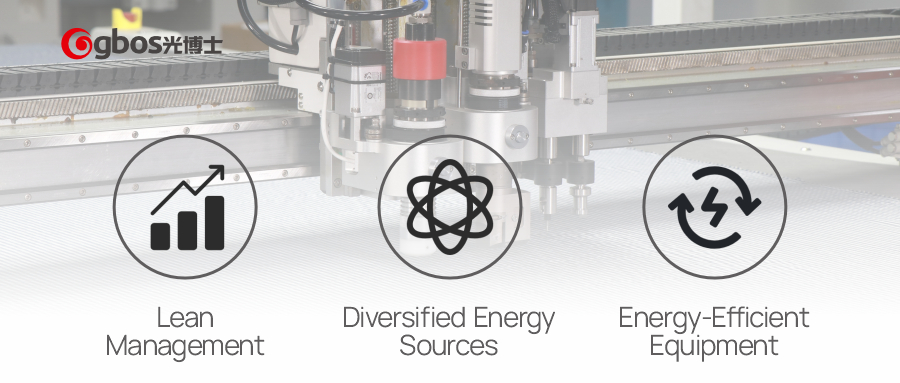
In the face of the current challenges posed by high energy costs, GBOS, as a flexible equipment solutions provider, actively supports the textile industry. Through data calculations, GBOS's oscillating knife cutting equipment demonstrates outstanding advantages compared to traditional cutting equipment, with just one GBOS device achieving or surpassing the efficiency of 2-3 traditional punching machines.
Furthermore, 1 GBOS oscillating knife cutting device can reduce electricity consumption by 120 kWh for every 10,000 cuts, resulting in significant energy savings.
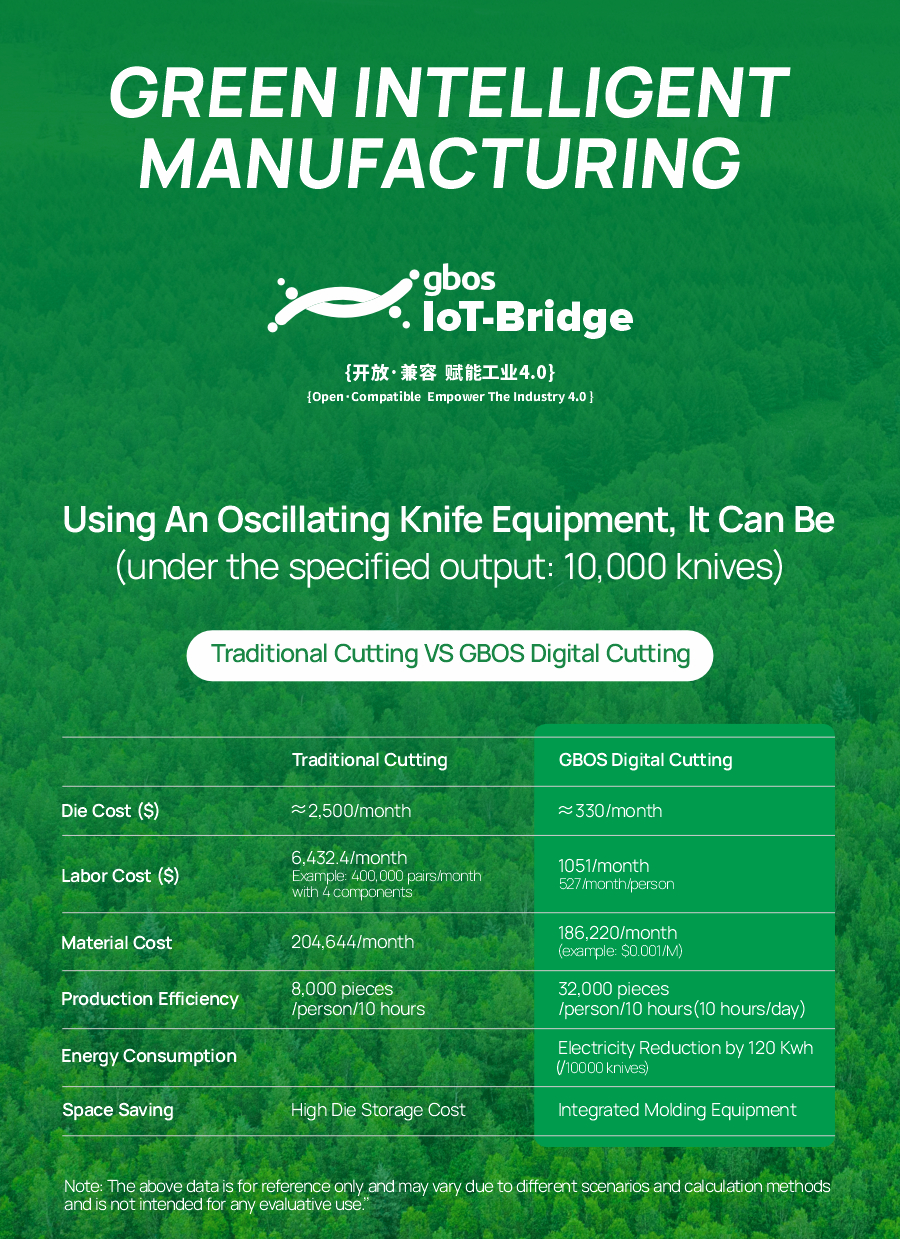
Amidst the increasing pressure on energy resources, GBOS understands that energy efficiency translates directly to a company's bottom line. We look forward to offering efficient energy-saving solutions to textile enterprises, helping them reduce energy consumption and achieve sustainable development!
Note: The first image is sourced from the internet, and we respect intellectual property rights. If there is any infringement, please contact us for removal.
Professional Digital Cutting Solutions
Smart Layout Planning | Sample Testing | ROI Analysis | Technical Support | Training | Custom Solutions | Parts